Here are a few easy to make blades, that don't require any specialized equipment, nor years of practice to make.
I just thought these examples might illustrate to our beginners, that quality knives don't have to be complicated. If you develop an interest in bladesmithing, the complicated stuff can come later.
Some of these are XX-Improved Plowshare Cable, forge welded into a solid blank, but most hunting knives I make are simple 10XX-series steels, mainly 1084 and 1095.
The blade with the curved antler handle is a modified Japanese grind, basically two flat surfaces, and pretty self explanatory.
The bolster on this knife is cast pewter. Basically, you wrap something like a strip of aluminum soda can around the end of the handle, followed by a few wraps of masking tape to hold it in place.
the melting point of pewter is very low, and it will solidify before it burns the tape off. Being a fairly soft material, it is easily shaped and finished after casting.
The hunting/skinning knives are convex-ground, which is most easily done with the "slack-belt" areas on a belt grinder. If you are using a belt "sander", there is usually a slack area above the platen,
and this is the area you would want to use to get a smooth convex grind from spine to edge. I like to keep my hunting knives roughly 1/8" thick through the tang area, with a progressive distal taper throughout the length of the blade.
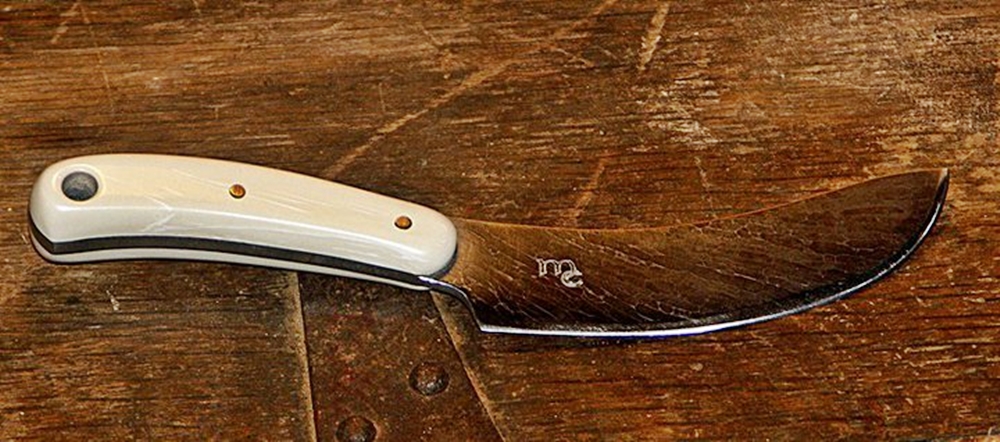
In my opinion, this is the strongest of the hunting blade cross-sections, and happens to be the easiest as well.
A convex grind, unlike a hollow-grind, or flat-grind, leaves more "meat" behind the edge of the blade, while still tapering down enough to give you an easily maintainable, razor sharp edge.
This is an easy grind to accomplish, although you must bear in mind that you still need a flat surface at the tang, so there is a certain amount of blending that needs to be done where the blade meets the tang.
To simplify them further, as you can see, I don't generally use guards. The shape of the back portion of the blade creates a guard on it's own, and from my experience with hunting knives,
a guard does little other than get in the way.
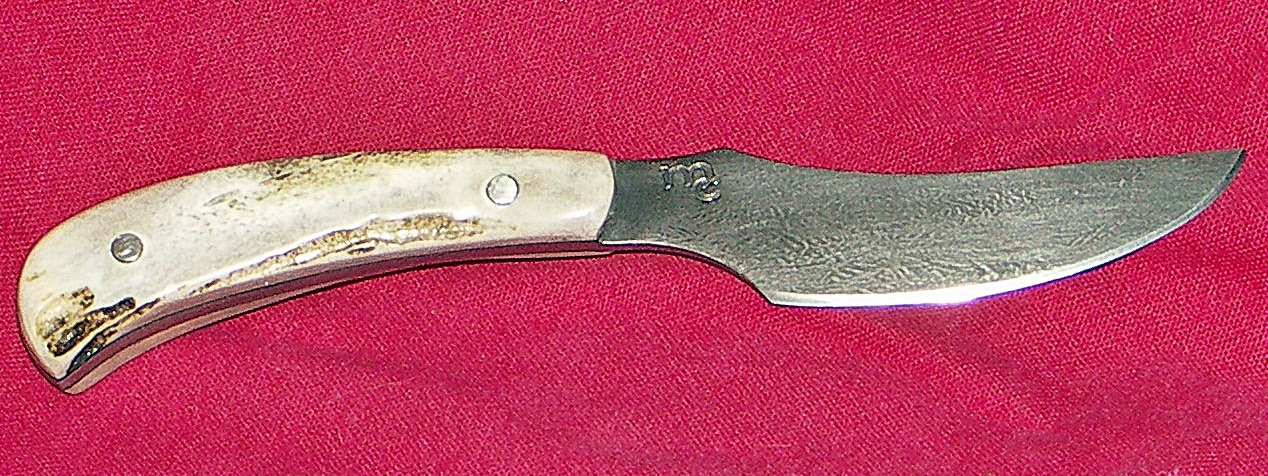
The Japanese-style Usuba is a specialty Chef knife, and since they are chisel-ground, they are "handed". This particular blade was made for a left handed person, thus the bevel is on the left side.
These are designed for precision cuts, so you do need a long, flat platen for an accurate edge. I grind these blades with the blade held in-line with the belt, and against a heavy platen to keep it as straight and
accurate as possible. These blades are thin (around 3/32"), and there is an increased chance of warpage during the quench, but they can easily be straightened after tempering, while they are still hot. I have forged them completely from 10XX series steel, but if you have a source of mono-steel (not Bi-Metal) power-hacksaw blades, they are already the perfect thickness for these blades. This particular blade was made from a 2"x24", M2 power-hacksaw blade.
Sean McGrath